3d Construction Printing for Affordable, Sustainable Housing
In Detroit, 48% of renters are considered cost-burdened, spending more than 35% of their income on rent. While Detroit has homes that are inexpensive to purchase, most of those homes were built before 1941 (60% of inventory) and are in need of significant and expensive repairs, making them expensive to heat and maintain. Our pace of building new, affordable housing has been too slow to keep up with demand at the low-cost end of the housing spectrum. While Detroit’s situation is more acute, it echoes the national trend, with some analysts estimating a 7 million home shortage for desirable, low-cost homes nationwide. A close look at the homebuilding industry reveals major themes that work against our ability to keep pace with the demand for housing at a price most people can afford.
In Detroit, total development costs are high and area median incomes are among the lowest in the country, requiring subsidies even to build market-rate rentals. And, it’s no wonder, since we build homes by hand much the same way our ancestors have done since 50 AD when timber framing was invented. The construction industry as a whole has been slow to embrace productivity-enhancing technologies common in the manufacturing industry, slower, in fact, than any other industry over the last 70 years or more.
Detroit has 75,000 vacant parcels in the nation's largest land bank, and the aforementioned barriers make building on them difficult.
Further confounding the pace of construction is a shortage of technology-skilled workers in an industry that has failed to attract young people and is hostile toward women. Construction work today is wasteful, contributing 40% to landfills annually. The homes we build require costly maintenance and contribute significantly to greenhouse gas emissions (7.5 tons of CO2 annually per household).
3d construction printing is a building method using a large-scale 3d printer. The 3d printing process begins with a 3d model, allowing for an inherently digital workflow.
3d printed structures are printed layer by layer, with no formwork necessary. The method reduces waste and requires less labor. 3D-printed homes are airtight, energy efficient, and disaster resilient. They require less maintenance over time and are less expensive to heat and cool.
This technology also has the potential to increase the use of sustainable and low-carbon building materials. There are already examples of homes printed with adobe (mud/straw) and wood pulp. As these materials become more widely available, we'll be able to incorporate them to build even more sustainably over time, with the ultimate goal being a circular economy.
Detroit renters are significantly cost-burdened, and while some Detroit homes may be inexpensive to purchase, they are expensive to repair, maintain, and heat and cool. Detroit, like many other cities around the country, needs more housing that its residents can afford. Typically, low-income individuals are not a part of the development process for new construction. Their voices are not heard. Decisions are being made by real estate developers who only care about upfront construction costs. Developers do not care about long-term affordability or single-family homes in walkable neighborhoods. Through our community engagement work, we know that these things are so important to Detroit communities.
The Citizen Robotics facility is located in Southwest Detroit, and we are embedded in the community there. The same goes for the neighborhood our first home is being built, Islandview. We prioritize engaging with the community and local partners above all. The first home we are building was informed by the community’s needs and desires. They indicated that they needed single-family homes for seniors to age in place in the community, so we designed it with that intent. We continue to bring community members into our facility to show them the technology and discuss how it can bring us to a future with more affordable, sustainable homes.
Our team has expertise in architecture, construction, digital fabrication, and advanced manufacturing. We continue to bring in collaborators where their unique expertise supplements our own, from sound engineers to building science professionals.
- Other
- United States
- Pilot: An organization testing a product, service, or business model with a small number of users
We've brought over 1,000 people through our facility on tours as part of our mission of expanding awareness.
We've done courses, programming, and workshops with 6 area universities.
We've done youth programming for over 25 kids.
By far the greatest barrier we face is a financial one. We are a non-profit, and the work we do is capital-intensive, and we have yet to make our full raise. However, we suspect this barrier has underlying cultural and market barriers that cause it. It is not uncommon for us to face a complete misunderstanding of this technology and its benefits. This technology is not more affordable than traditional construction methods yet. However, we know with the right investment it will get there. We need people who don’t just care about the bottom line, people who care about innovation, about building better, more sustainable homes. We believe that Solve will help us to find these people.
- Business Model (e.g. product-market fit, strategy & development)
- Financial (e.g. accounting practices, pitching to investors)
- Human Capital (e.g. sourcing talent, board development)
What makes our approach truly transformative is how our programming sets up a virtuous cycle of impact. The more we recruit and train within the community, the more construction workers become available. The more accessible we make 3d concrete printing, the faster we can build homes. As we create more real estate development opportunities for these new, digitally-fluent, super-productive workers, we gain more and more affordable homes. This increase in the supply of quality, affordable homes lowers the cost burden for residents and paves the way for expanding equity through homeownership.
This technology is also a lever for change in how it can meet up with other technology. For example, we used a digitally fabricated roofing system. We could do augmented reality walk-throughs before it's even built. Our six-axis industrial robot could paint, mill, and more.
The future of printable materials is exciting as well. The range of 3d printable materials is expanding rapidly. Material formulations are just now becoming available that contain less cement, and there are 3d printable materials that contain no cement at all. Others have proven that it's possible to print with materials from the waste stream such as recycled tires or plastic, among other things. The ultimate goal is to use materials that are part of a circular economy, like wood pulp and hemp. Our demonstration will be an opportunity to discuss all these material options and more, working our way toward more sustainable 3d printing.
- Create a sustainable ecosystem for building low-cost, energy-efficient homes
More young people and women enter the construction industry
Expanded adoption of 3D-printed construction
More new, affordable homes with fewer subsidies needed for their construction
More Detroiters rebuilding Detroit
- 1. No Poverty
- 3. Good Health and Well-being
- 4. Quality Education
- 8. Decent Work and Economic Growth
- 9. Industry, Innovation, and Infrastructure
- 10. Reduced Inequalities
- 11. Sustainable Cities and Communities
- 12. Responsible Consumption and Production
- 17. Partnerships for the Goals
More young people and women participating in homebuilding, enrolling in training programs, attending Citizen Robotics workshops, and assisting on Citizen Robotics projects.
More supply of affordable, sustainable housing.
More 3d printed construction.
Reduced material waste in the homebuilding industry.
Less pollution from our homes and the construction of them.
Higher wages in the homebuilding industry.
Increased use of productivity-enhancing technology in homebuilding.
More jobs available in 3d construction printing.
More small 3d construction printing businesses.
Higher proportion of low-income individuals living in adequate, safe, affordable housing.
Citizen Robotics increases awareness of robotics in homebuilding. Citizen Robotics provides training in 3d construction printing. Trainees learn about digital processes in homebuilding, 3d modeling, 3d construction printing, rapid prototyping, and more. Trainees are skilled up and earn higher wages. Trainees go on to start their own 3d construction printing companies. Increased robotics in homebuilding requires fewer laborers, filling the gap of the labor shortage in the construction industry. Automation and digitalization in homebuilding lead to lower construction costs. Lower construction costs lead to more affordable homes.
Increased use of 3d construction printing leads to less construction waste.
Since 3d construction printing can create airtight homes with high thermal mass, we create homes that require less energy to heat and cool so that the homes we build contribute less CO2 emissions from daily living.
3d construction printing is a building method using a large-scale 3d printer. The 3d printing process begins with a 3d model, allowing for an inherently digital workflow.
3d printed structures are printed layer by layer, with no formwork necessary. The method reduces waste and requires less labor. 3D-printed homes are airtight, energy efficient, and disaster resilient. They require less maintenance over time and are less expensive to heat and cool.
This technology is also a lever for change in how it can meet up with other technology. We used a digitally fabricated roofing system, we could do augmented reality walk-throughs before it's even built. Our six-axis industrial robot could paint, mill, and more.
- A new application of an existing technology
- Manufacturing Technology
- Materials Science
- Robotics and Drones
- Software and Mobile Applications
- United States
- Nonprofit
We plan to make our training and innovation center accessible to all, regardless of gender, race/ethnicity, religion, or disability. Our first webinar in 2020 was to NOMA, National Association of Black Women in Construction, and Michigan Minority Contractors Association. Reaching out to and including these diverse groups will make it possible for us to recruit a diverse board and membership. Our team shifts as our interns go back to school or move on to other opportunities, but we consistently value diversity. Our team has consisted of people of color, immigrants, LGQBTQIA+ individuals, women, and individuals with disabilities.
We appreciate that all great construction projects respect local context, needs of the neighborhood, culture, climate, soil conditions. As such, we begin our builds with community engagement even before conceptual design. Diverse input creates strength, staying power. Our build project in a Detroit neighborhood, even though it’s just one home, began with a call to the local CDC to better understand what they thought was needed in their own community. We are actively working with an architect from NOMA on that home, and we have continued to interact with NOMA, including providing them the first tour of our first build. Our first home, designed as a place for a senior citizen to age in community, is visitable, and we plan to make our next build visitable as well.
We will continue to make improvements in our DEI efforts as we learn from our membership, staff, board, and program partners. We recognize that robotic construction may be a space in which those with disabilities have felt excluded. From 3d modeling to robot programming, there are many opportunities and we hope to open the door for all.
Citizen Robotics is a nonprofit that expands awareness of and creates access to robotic construction techniques in homebuilding, especially 3d construction printing. We attract young people to the home building industry and train them in digital tools, 3d printing, rapid prototyping, and more. Through the same training, we skill up the existing construction workforce, allowing them to earn higher wages.
We can impact the affordable housing crisis only as fast as the technology can be adopted. The Citizen Robotics business model is to create a movement around 3d printed construction by both building with the method and sharing our success using the construction method. We know that adoption is encouraged first by expanding awareness, then by creating access and training. Once the community has the capability to build homes this way, they will begin to print homes for themselves.
In our facility, we seek out the highest and best use for robotic construction techniques. We experiment with homebuilding, green stormwater infrastructure, stoops, hardscape, and beyond. In this way, we're able to show people the broad opportunities in robotic construction.
- Individual consumers or stakeholders (B2C)
We plan to bring money in to fund our work and mission through sustained donations and grants, selling 3d printed hardscape and wall segments for housing, printing for other artists, makers, and more, and training programs.
We have received a grant from the Ford Foundation. Our first build is partially funded by the Michigan State Housing Development Authority, and is midway through completion. We have provided workshops, one of which was funded by Applebaum Family Philanthropy. We have sold hardscape elements to local companies such as Ideal Group, SDEV, and AGI Construction.
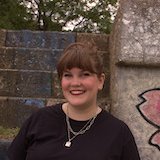
Co Founder and Communications Director