Sena Leg - Sustainable locally made prosthetic legs
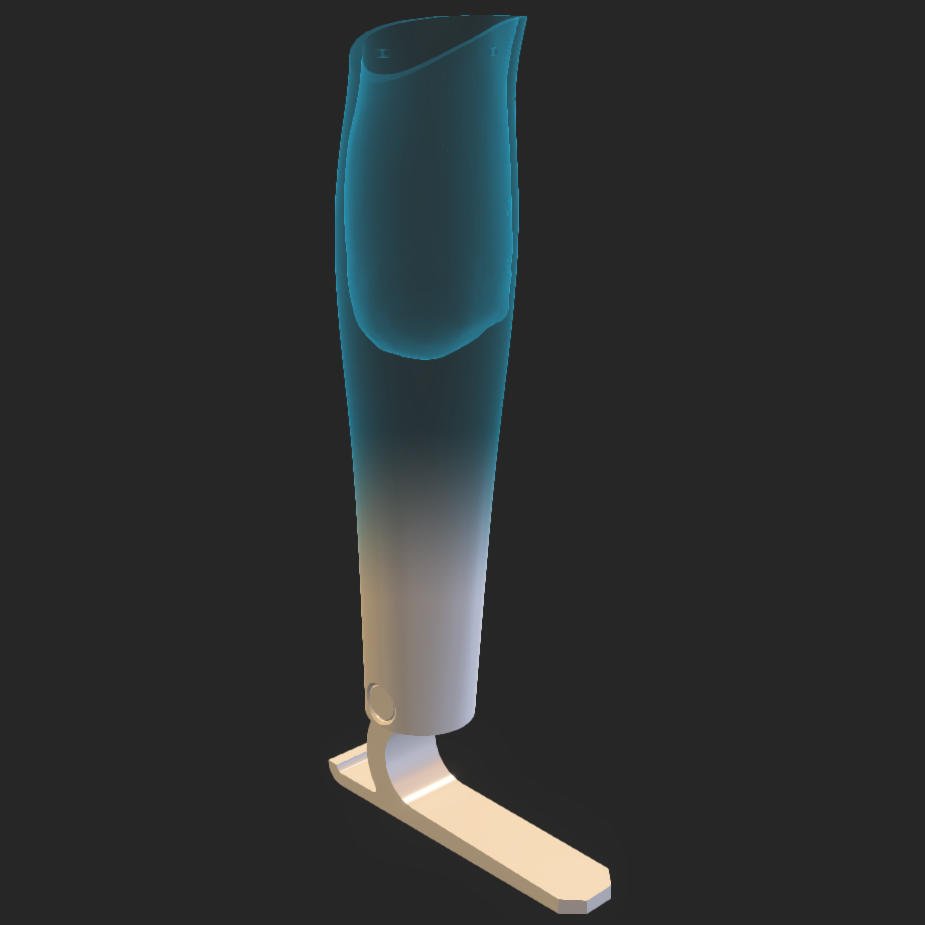
Ghana has a need for low-cost prosthetics because the amputation rate in the country is increasing due to auto accidents, alternative medicinal practices and diabetes. If a person is missing a leg it also ties up both their arms with crutches and makes it difficult for them to work.
Ghana also does not have a strong local manufacturing and design sector - especially with new technologies such as 3D printing. This hurts them even when they receive donated equipment; when it breaks, it's difficult to source replacements.
The Sena Leg solves both these problems. It is a low-cost sustainable prosthetic leg that will be designed and manufactured locally using a training plan that teaches Ghanians how to design and create complex products.
Doing this empowers Ghanians to create their own industry and literally get back on their feet.
We are solving two combined problems; a lack of access to design skills and a lack of affordable prosthetics.
An increase of amputation rates in Ghana can be attributed to poor diets, lack of access to health care, vehicular accidents, and peacekeeping operations by the Ghanian military.
Impact of Amputation on the community:
School challenges: Kids who gets amputated early on in childhood has more challenges in school. They have low mobility, unable to participate in school activities and decreased chances of graduating on time. There is increased dropout rate in such students.
Social interaction and mobility difficulty: For adults, maneuvering with both hands on crutches while doing daily tasks is not a menial task. It hampers their social interaction and in a country where social interaction is very strong.
Unemployment: With low physical mobility and limited access to public transport, amputees can face difficulty in finding jobs to support themselves with.
With the focus of this project also being skills transfer, the knowledge of how to use Computer Aided Design (CAD) will educate Ghanians on how to create their own replacement parts for donated equipment and also help them develop their own industry and be less reliant on external sources.
Children and adults in Ghana who have either had a limb amputated. Entrepreneurs, craftspeople, students and retraining adults who want to learn advanced design and manufacturing techniques.
Our solution is to create a sustainable 3D printable prosthetic leg that is:
1) Low-cost, easily manufactured, highly customizable. This leg is meant to be produced on any machine that can get up to a hot end temperature of 245° C.
3D printing means it can be produced on a per-user basis. A free software-based toolchain (based around Fusion 360) means low investment, and wide tolerance allowances means it can be manufactured on low-cost 3D printers.
Finally, by using the Structure scanner from Occipital, the maximum investment in scanner hardware can be as low as $400. Feasibly, with the printer and a capable computer the total investment can be as low as $1,500.
2) Sustainable, closed-loop, zero waste. This means no support material and using only materials that are either commercially compostable or easily recyclable.
3) Easy to design and build. This project is meant to be a showcase to teach people in Ghana how to use CAD and 3D printing so they can design and manufacture their own solutions in the future. So along with the leg comes a curriculum and training on how to do it themselves.
- Support communities in designing and determining solutions around critical services
- Create or advance equitable and inclusive economic growth
- Prototype
- New application of an existing technology
While others are working on 3D printed prosthetics, these key features set our solution apart:
1) Our project is a leg; a very performance-critical type of prosthetics. Other open-source projects like e-Nable have focused on hands because their performance under strain is not as mission-critical.
2) Our project is open-source. Other 3DP prosthetic companies exist, but our design will be free to use. Our software toolchain is mostly free and/or open source as well. Nia Technologies is a 3DP project similar to ours, but they built their own proprietary software.
3) We are unique in that the project is education and empowerment focused. Our curriculum will teach people how to design and make this leg as well as similarly complex objects on their own in Ghana and elsewhere.
4) The Sena Leg is designed to be completely 3D printed on consumer grade hardware, meaning simple supply lines and easily fixable machines. Companies like Prosfit and Mecuris are designed for industrial machines. Nia Technologies does use home printers but their designs are mostly limited to children, whereas ours will target the whole age spectrum.
5) The Sena Leg is unique in that it has been designed from the beginning with a focus on sustainability. We chose PETG as our main material for the leg – a common and easily recycled plastic. Most importantly, our manufacturing process is zero-waste; there is no support material required when printing – a common waste source with 3D printed products.
Our solution utilizes inexpensive 3D scanners, 3D printers and free or open source software.
Our materials (PETG and biodegradable TPU) are printable on any machine with a heated build plate - a popular example is the Ender 3, which costs $200. For $500, the Creality CR-10 can also print the entire leg in a single piece.
The 3D scanner we are using is the Structure Sensor from Occipital, which is easy to use and costs $400.
The software we are using is Fusion 360, which is free to individuals and startups, Meshmixer which is completely free and Instant Mesh, which is Open Source.
Lastly, should we secure funding we would like to utilize generative design to create a "fill in the blanks" design process for developing customized prosthetic feet.
- Artificial Intelligence
- Biomimicry
Our solution is cheap enough to be made anywhere, simple enough to be made by anyone and can be made on inexpensive equipment, meaning it can be distributed widely. It uses inexpensive materials and can be customized to fit any number of users.
It is a good project for people to learn how to design their own solutions and the training provided will help them to become expert enough designers to apply their 3D design skills to other entrepreneurial pursuits.
- Very Poor/Poor
- Low-Income
- Middle-Income
- Refugees/Internally Displaced Persons
- Persons with Disabilities
- Ghana
- United States
- Ghana
- United States
We are not serving anyone yet because we are finishing the prototype. Afterwards, we will test with one and then grow to 20 in year. Within five years we hope to be serving thousands by making the technique open source and distributable.
Next year:
Complete prototyping and training staff in Ghana on 3D design and printing. Fit 10 test users with the leg.
5 years:
Establish a sustainable business mass producing prosthetic legs for communities in Ghana and beyond. Build an online distributed community of makers serving their local community’s needs. Create the generative algorithm for designing the prosthetic foot.
Barriers:
Mechanical testing of our prototypes.
Establishing a network of available biomechanical professionals.
User testing in Ghana.
Funding for transportation of project leads between the Sena Institute of Technology in Ghana and the United States.
Consult and partner with mechanical and biomechanical professionals.
Partner with local hospital, St. Anthony Hospital in Ghana.
Seek funding through grants and crowdfunding.
- Other e.g. part of a larger organization (please explain below)
The Sena Leg is the foundational project for the FabLab within the Sena Institute of Technology in Ghana. SIT is registered as a 501(c)(3) in the United States.
Two:
1) Andrews Akwasi Agbleke
2) Jordan Thomas Pelovitz
Jordan is a 3D printing and design expert with years of experience in the field. Andrews Akwasi is a postdoctoral researcher at Harvard and has a strong network of local business leaders and medical personnel.
1) Sena Institute of Technology, Ghana is providing local resources and connections with people in the community for training.
2) MIT fab lab community network is providing certification and resources for the Fab Lab being set up at S.I.T.
3) St. Anthony hospital, Dzodze, Ghana will be working with us to provide prosthetists and patients.
Once the design is ready we will make a contract with Ministry of Health in Ghana to distribute the Sena Leg to hospitals across the country and in areas that it is needed.
At the same time we will also be searching for donors, grants and crowdfunding.
We will also roll out our subscription plan to work with other local African hospitals and eventually maybe Western hospitals as well.
Finally, we will create an online configurator that will allow people to create customized graphic shells for their prosthetic to give them a unique look. These customized prints will be provided for an additional price.
One of our reasons for getting funding will also be the maintenance of the open-source design. The training will be provided free of charge as part of the Fablab being built at S.I.T.
Through sales to governments and private individuals.
Grants and donor funding.
Offer services to hospitals such as printing and scanning support & modeling the prosthetic.
Customizable prosthetic cover.
Crowdfunding.
To reach our goals, our team seeks partnerships within Solve to:
- Develop a strategy to expand the reach of our solution beyond just Ghana.
- Consult on building a business plan around an open-source hardware solution.
- Find funding to build the FabLab at the Sena Institute of Technology.
- Locate engineering talent to develop a generative algorithm for foot design based on the prosthetic user’s weight.
- Develop a strategy for working with similar groups to combine efforts.
- Business model
- Funding and revenue model
- Talent or board members
- Monitoring and evaluation
- Media and speaking opportunities
Hospitals, NGOs and prosthetic manufacturers.
We would use the prize to develop a generative algorithm for designing the prosthetic feet based on the user's desired weight and springiness level. This would dramatically increase the ease of design for our project and open it up to being used in more places with less training.
We will use the prize to pay for fatigue testing, engineering design work to create a "fill in the blanks" generative design system for creating prosthetic feet. We would also like to utilize this money to pay a developer to help create our prosthetic configurator application.
N/A
N/A
N/A
We will utilize this prize to complete the construction of the Fablab at S.I.T.
N/A
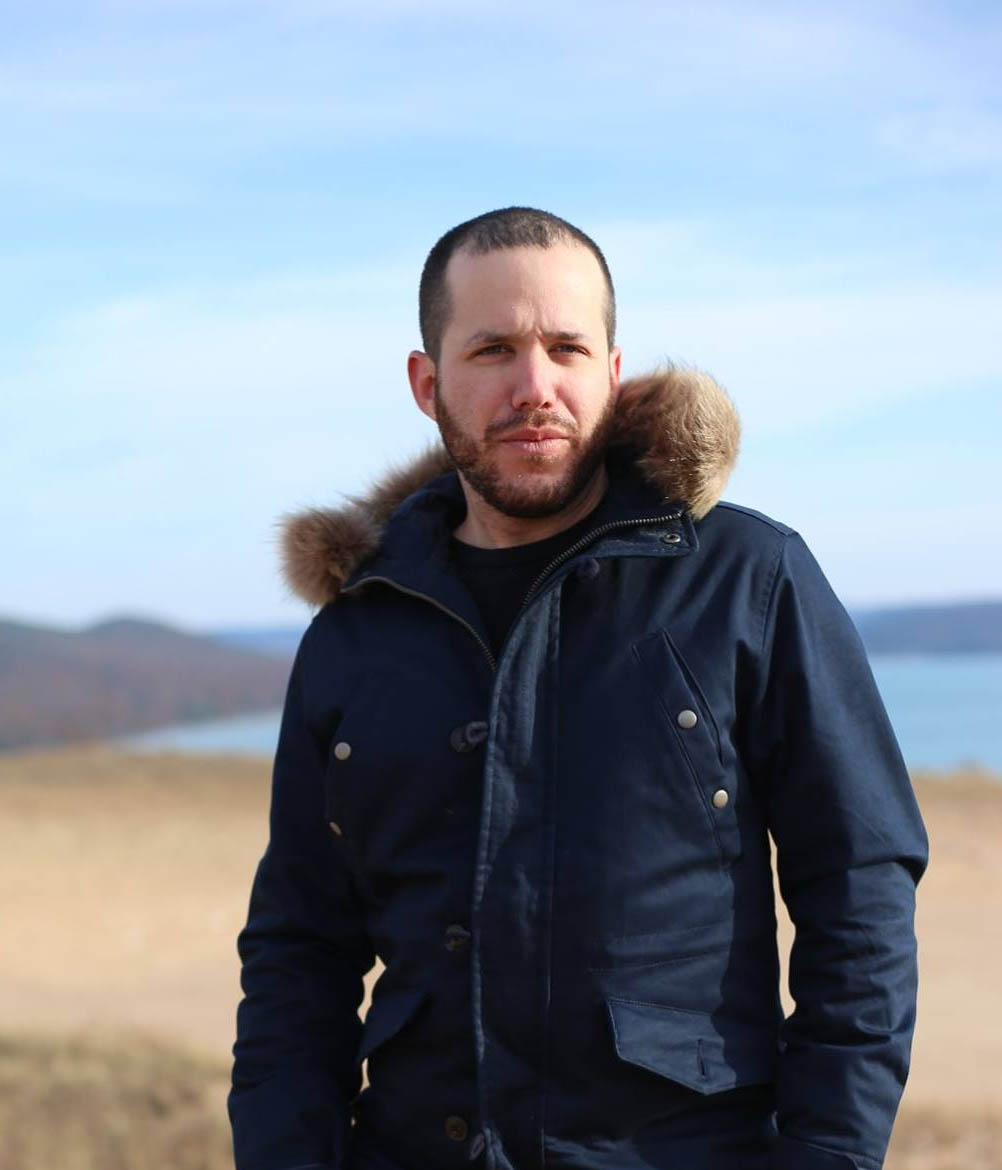
Chief Designer
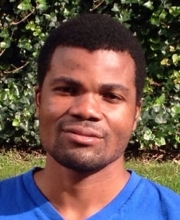
President